
Entry Canopy Lucknow Hotel Tulip INN Uttar Pradesh-Tensile Structure Fabricators

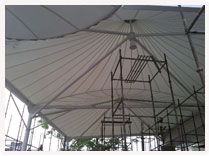
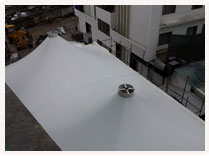
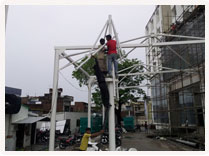

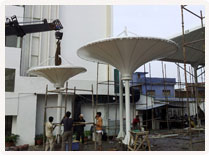
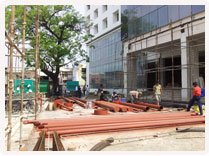
|


In the Heart of the City of �Nawabs�, established Business house operating 4-star hotel Tulip Star Plan an expansion with added capacity of 200 Rooms in the 5-star category in an open plot attached to existing Hotel.
The requirement was to seamlessly integrate old & new facility with all weather roof covering to allow all season movements for Guest & service staff.
The challenge here was to be within frame work of local development control body regulations, apart from strict restrictions from fire departments interns of minimum height of the structure, clear unobstructed entry ways for fire engine movements in case of emergency.
There was a huge off set between old building & new building due to set back rules for the new developments. Hence the entry ways of the 2 structures were out of line by at-least 10 meters. There were no CAD structural details available for now cladded old building. Also there were no drawings prepared with details showing both old & new buildings. As we operate from Mumbai Design office, in a limited time available during visit of our director, Mr. Anil Shah it was not possible to carry out detailed survey. The customer though had an Architectural department apart from team of site engineers, could not allocate resources to give us details of existing & proposed structures.

In Absence any structural details for old Buildings, Challenge was to design a Tensile Fabric Roof with almost no structural columns along Fire engine pathway, at the same time taking No support from old Building. The civil work for the new building did not follow best workmanship practices. So the even bigger challenge was to fabricate modules at our workshops & assemble seamlessly at site without modification and delay. The unprofessional Project team, PMC team, supporting Admin team & overall culture of the hospitality company made things worse.


The total open Area of a Five Star Hotel In Lucknow, Uttar Pradesh to be covered was roughly 425 sq. meters.


Our Tensile Structure Manufacturer team smartly divided the Area in to2 different zones. Rather than trying to align the skewed entrances we suggested 2 different Fabric canopies individually aligned to respective Hotel Buildings. The connection was established with series of overlapping Inverted cones again in Tensile Architecture.
As we must High-light entry canopy of the New Hotel Building, we suggested Tensile membrane Architectural design form having 2 inter connected, slanted cones. The Hotel orientation demanded Trapezoidal shaped entry canopy divided in to 2 non equal connected conical Fabric structures.


The entry canopy was designed to start from the new building from a beam running across the suggested entry leading to Reception lobby. Total span of the canopy was 20 meters, with an intermediate RCC column right in the middle. Sufficient slope of 200 mm. (angle ) was introduced along the length of canopy so that water can move to the outer edges of the entry canopy. The Tensile fabric canopy was supported on the outer edges by 3 Steel columns which inturn were fixed on the RCC beam casted along the boundary of the proposed Hotel Plot. The Height difference of 1 meter was introduced in the canopy with over-hanging span varying from 12 meters to 22 meters.
Detailed Analysis of the structure was carried out with Internationally acknowledged FEM software. In absence of Local codes for Governing construction of Tensile Fabric structures, British standards were followed to generate wind loads depending on geometry, height of structure, height from sea level, dist from sea, surface roughness, topography etc. The wind pressure for wind speed of 110 km/ Hr., followed by various factors to take care of the variable mentioned above were used.
Once structure was analyzed by our Tensile Structure Fabricators team, the dimensional detailing of each individual structural members were carried out after STAAD analysis depending on the max. load generated in load combinations. Auto cadd 2011 was used for Detailing- drafting purposes.


The primary structure was selected to be hollow tubular square sections 150 X 150 mm in size , for all the beams. whereas vertical columns were fabricated from round hollow section of 219 mm dia. X 8 mm thickness. The top flat edge of the 150 X 150 mm beam was smartly used to fix the fabric fixed edges & electrical supply wires for RGB LED lighting.
The top ring Dia. 600 mm supported on Dia. 115 mm Mast which in turn was supported by 4 radial members from each of the corner, having Dia. 140 mm through a Sliding joint in the center to enable pretensioning while Tensile Canopy installation.


The Ferrari 902 S 2 , PVC coated fabric was patterned Radially in all 30 / 36 patterns, depending on the size of the cones. To absorb higher stresses towards the Ring center the fabric was reinforced with another layer of 902S membrane patterned in floral shape.
The fabric was fixed on the Top edge of the square Beams with the help of clamping stainless steel strips of 40 mm X 8 mm, separated by Neo-perene rubber Gaskets, with help of Self threading extra large screws. The fabric was clamped to the central Beil Ring with help of Stainless steel Nut bolts.


The Foundations were the responsibilities of the purchaser. The steel structure was pre- fabricated in modules in our workshop based on the details received. The Exact Foundations details were send to purchaser to cast the foundations in advance. The whole modules were transported to the site. There were huge deviations in the RCC structures of the New Hotel building including Non aligned beam on which the canopy would start. The Height of the beam was different from what was conveyed to us. The design was amended on the spot. Accordingly the ready modules were corrected on the spot. The foundation was casted AFTER the material reached the site. The scaffoldings were simply not in the right conditions. The Availability of Cranes/Hydra services were limited. The rentals were on a shift or a day basis rather than on Hourly basis. Still our Tensile Structure Manufacturer team managed to erect the structure in a record time of 7 days. Our Tensile Structure Fabricators team erected inverted umbrellas steel structure even though the foundations were just not casted.
We deputed our Painting team to complete the epoxy coating as planned. We were running against time specially with monsoon fast approaching. We completed painting. Took the site final re-survey before remodeling for patterning - welding. The Fabric now welded was delivered in next 10 days. We send team again for the final Tensile Canopy installation. The Hotel was far from ready. As soon as our team landed, the first seasonal rains started lashing the city. Our challenges to have a safe accident free installation multiplied. Clean uncluttered floor area to spread - prepare fabric was just not available. vehicles from employees & Vendors made our task most difficult. The Purchasers were in different world dealing with other site related issues as the rains made their life miserable.
We requested for a crane which never arrived. We were determined to complete the installation. As soon as rains stopped we prepared floors, laid plastic sheets, the fabric was unwrapped, the beil ring was fixed. We called the crane & 48 hours non- stop installation began. The lifting & fixing the Top rings (2 rings on the same single fabric ) took more than 8 hours. We immediately started fixing the fabric on to the RCC beam first. The rains at regular intervals would make our job much more complicated. We managed to clamp all the fabric edges in 30 hours. We lifted the fabric up to avoid ponding. We took a break at 4 a.m. so that our team could take a short sleep.
When Team got up at 8 a.m., It had already rained. As the Top rings were not fully lifted, the water was ponding at 2 areas. One behind the cones towards the hotel building & all along the lower edge. Luckily we were up in nick of time. It took us 2 hours to remove more than 1000 liters of water from the top of fabric. We lifted fabric further up with help of Hydraulic equipments; this removed all the water from the canopy. And we took a sigh of relief. The rest of Installation was not as critical as inverted cones have no possibility of pending. As the conical fabric was mechanically joined radically at the site with primary structure assembled, it took more than 8 hours to complete each cone installation. Never the less it was a great challenging experience for us to install the fabric in an unfriendly conditions. It has taught us many lessons. We have incorporated many design changes in all our future projects so that we can keep installation pace at highest & Avoid troubles in case it rains. Also we have learnt quite a few lessons specially managing outstation projects in smaller Cities/Towns.


The project of a Five Star Hotel in Lucknow, Uttar Pradesh was completed well within time span of 35 days. The steel structure was installed at site in 7 Days even in unfavorable conditions. The Fabric Installation was carried out in Rainy weather. Final fabric Installation took just 72 hours back to back.
